Quick Guide to Industrial Pumps
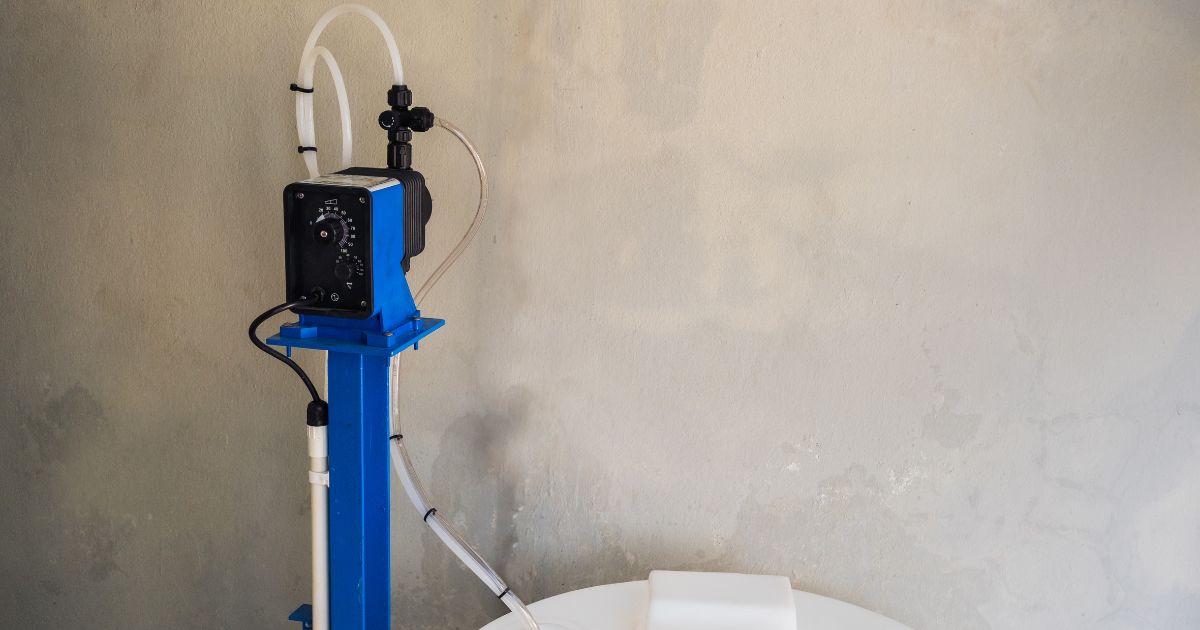
We’ve been getting enquiries about pumps and fluid handling products, so we thought it would be a good idea to put together this non-technical and simplified selection guide.
- Common types of pumps
- Primary pump selection considerations
- Secondary factors that might affect your setup
- Special considerations for Australian industries
- Preventative maintenance of industrial pumps
Common types of pumps
Take note of their differences in design and intended purpose. You can’t use just any pump to handle / transfer any liquid.
Here are some popular pump types we sell for industrial applications:
- Chemical pumps are fluid transfer devices designed to move liquid chemicals from a large container (eg a drum or IBC) to smaller containers, or into a process. Hand drum pumps consist of an immersion tube connected to a (positive displacement) PD mechanism to siphon the liquid content. They are commonly used in petroleum, pharmaceutical, food manufacturing and cosmetics/personal care manufacturing applications.
When selecting a chemical pump, it is critical to review the manufacturer’s compatibility data to ensure the chemical you are working with is compatible. In some cases, such as acids, this will not just come down to the chemical, but also the concentration. - Diaphragm pumps are PD pumps that utilise flexible membranes, called diaphragms, to move and transfer liquids. They typically have two chambers that siphon and discharge fluids in an alternating sequence that results in one continuous exit stream. They are available in either manual or air-operated double-diaphragm (AODD) variants that can be used in dewatering, moving slurry, sludge and in other low-pressure liquid transfer applications.
- Fuel pumps are used to transfer fuel from bulk containers such as drums or totes. They generally consist of a suction tube or hose, a pump mechanism, and a delivery hose with a fuel nozzle. They are used in various industries such as transportation, pharmaceutical, beverage and chemical handling, among others.
- Hand-operated fuel transfer pumps require a lever to be manually turned to operate a rotary or lobe assembly to displace and move fuels and other liquids.
- Electric fuel transfer pumps and bowser pumps, on the other hand, use either AC or DC electrical power source to operate its displacement pump.
- Grease pumps consist of a suction tube, drum cover, pump assembly, and delivery hose that are intended to transfer grease from bulk containers (eg. Drums) to smaller vessels or directly into the system. They can either be hand-operated or compressed air-operated. They are commonly used in farming, construction, heavy machinery and other industrial applications. (Grease guns are a good alternative for hand-held, light-duty applications.)
- Oil pumps are designed to transfer oil from bulk containers to smaller vessels or directly into a process. They consist of a suction tube that may be hand-operated, air-operated, or electrically operated. A delivery hose, often with a nozzle, directs the discharge of oil. They are available in different configurations to suit various container sizes. Some models, such as these examples from Macnaught, are even battery-operated. They are commonly used in maintenance and repair workshops.
We also sell pumps for common household and general use:
- Drainage pumps, sometimes called sump pumps, are submersible pumps designed to move water out of a water-collecting basin or pit that are commonly installed in areas below ground level, such as household basements. They usually have a mechanism (eg a float) that detects “flooding” and activates the pump when water levels reach a certain threshold.
- Household pumps are a wide selection of general-purpose pumps that are marketed as multi-stage pumps, pressure pumps, rainwater pumps and surface-mounted bare pumps. Some models are even submersible, while other examples -- such as pond pumps that are designed for pond circulation and ornamental fountains -- may be continuously operated in either vertical or horizontal positions. They are commonly used in agricultural irrigation, backyard farms, farmhouses, gardens and pools.
Primary pump selection considerations
We may ask you these primary questions to help you determine the pump you need.
- What kind of fluid will be passing through it? You may need different pumps to deal with chemicals, oil, slurry and even water. The viscosity of the fluid is also a major consideration. For example, some of the most viscous ones like oil could more resistant to flow. The corrosiveness, (possibility of) presence of solids in and temperature of the fluid are important factors to consider, too.
- How far from the source will it be installed? This has to do with how hard the pump should work to “pull and push” the fluids through it. This has something to do with head pressure, so you want to factor in the height to which the fluid needs to be 'lifted' and the overall resistance of the system (due to pipe lengths, bends etc).
- What is your required power rating? This -- together with the flow rate and 'distance from source' (previous point) -- has a lot to do with your selection, as they affect the efficiency, longevity and reliability of the entire pump system.
- What is your required flow rate? Refer to the previous point. You can measure this in litres per minute or cubic meters per hour to determine the needed capacity. By the way, make sure you measuring it with a flow meter?
- What is your required discharge pressure? This is the total pressure energy, measured in megapascals (MPa), that the pump needs to work with to pass fluid from the source through the entire system. Essentially, this is the amount of force needed to overcome resistance in the system. This is largely affected by the diameter and material of pipes and also by the viscosity of the liquid passing through it.
- What material should the pump be made of? Ensure the pump is compatible with the fluid to avoid corrosion and damage. Options include cast iron, stainless steel, and various plastics.
- Does the pump have to be self-priming? Some designs make it hard and very inconvenient to manually prime.
Secondary factors that might affect your setup
Here are other secondary factors that may have a significant effect on your setup:
- Concentration and temperature of the fluid (especially if they’re chemicals)
- Distance of pump above or below the reservoir
- Inner diameter of the suction pipe(s)
- Inner diameter and length of the pipes, elbows and valves
- Frictional resistance points in the entire system
- Maintenance (ease of access, parts availability and required frequency of maintenance)
- Power source (electric motors, diesel engines or hydraulic power, depending on the application and site availability)
- Quality of the components in the pump itself (eg bearings, gaskets, lubricants, seals etc.)
- Sealing (mechanical seals or packing types must match the liquid and operating conditions)
- Static height (the height between the suction pipe to the highest point on the entire pipe run)
Special considerations for Australian industries
- Agriculture: Pumps for irrigation need to be energy-efficient and handle large water volumes, sometimes with solids.
- Manufacturing: Consider the fluid type, pressure requirements, and desired level of automation in the manufacturing process.
- Mining: Durability, abrasion resistance, and ability to handle slurries are critical in mining pumping applications.
- Water and Wastewater: Pumps need to handle fluctuating flows, solids (in wastewater), and corrosive environments.
Preventative maintenance of industrial pumps
Pumps are not cheap to replace, so you might as well make sure it’s always in good condition and working properly.
Some things to check regularly:
- Clogging: Solid particles -- such as dirt, grime, mud, rocks, sand and other debris -- may inevitably get stuck somewhere in the system and block components. Such blockages can increase friction, pressure and operating temperatures that place additional load on pump motor. This is quite common when you don’t have a filter installed before the pump or the suction pipe. A sudden drop in flow usually tells you there’s a clog somewhere, assuming all else is working (eg. there is power going to the motor).
- Corrosion: Visually inspect for cracks, discoloration and rusting on pump assembly and pipes. It’s also best if you can occasionally look at the condition of the internal components, such as the impeller. Corroded pump systems can also contaminate the fluid.
- Excessive noise and vibration: Make sure it’s minimal and within the tolerable design limits. While a low humming sound is quite normal for most pumps, loud clunks usually tell you there’s a problem somewhere. In addition, too much vibration is usually caused by impellers that are damaged, misaligned or improperly installed/balanced. These could easily damage your pump and its motor.
- Excessively high temperature: If the pump gets hot beyond “normal operating temperatures”, there must be a problem somewhere. Common suspects are motors running inefficiently for extended periods. Is there a clog somewhere?
- Flow rate: You should be monitoring the system’s pressure constantly. While some drops and surges in pressure are acceptable (depending on the fluid and system set-up), intermittent wild fluctuations may tell you that something needs further inspection in the system.
- Leaks: When something starts leaking somewhere in the pump and pipes, your first suspects will usually be gaskets and mechanical seals, as they’re often the weakest “links” in such a pressurized system. They’re meant to experience wear and tear anyway, so expect to change them regularly. Aside from the gaskets and seals, you may also find leaks in the hoses so check them as well.
- Lubrication: Make sure to regularly grease the bearings and other moving parts but be careful not to over-lubricate them.
In a nutshell
- Choose your pump according to its design, purpose, proper specifications and the type (and viscosity) of fluid that will pass through it.
- Consider how far you will install the pump from the suction pipe to the fluid’s destination matters, especially to ensure its efficient operation.
- Always monitor the pump system's overall health by checking for clogging, corrosion, excessive noise and vibration, excessively high temperature, flow rate, leaks and lubrication.
Pumps can serve you well for a long time, so long as you choose the right one for the job and take preventative measures to keep it performing as expected.
AIMS’ Note on Buying Industrial Supplies
- Breadth and depth of brands and categories: Go with a supplier that offers a wide range of reputable brands across multiple categories and sub-categories.
- Bulk purchase discounts: For large orders, check if you can take advantage of volume leverage. Some suppliers offer business accounts* that give you access to special pricing (volume discounts), preferential support and even credit eligibility (subject to supplier approval, terms and conditions).
- Product and service information: Evaluate the completeness and usefulness of data in their online product listings. Prudent suppliers will include as much useful information as possible to help you assess and compare products. In terms of service info, the supplier’s FAQs (if any) will give you a good idea of their standard policies*, processes and commitments.
- Promotions: Check for ongoing promotional campaigns so you can get the best prices. Many suppliers run regular discount-based promos. Some can point you to government-hosted rebate programmes like the SafeWork NSW $1000 Small Business Rebate.
- Safety compliance: Make sure the product in question meets Australian safety standards and regulations, especially if there are relevant compliance requirements or work health and safety (WHS) laws that apply to your business or state. Look for relevant certifications and markings where necessary.
- Supplier reliability: Choose reputable suppliers with a proven track record of delivering quality products and reliable customer service.
- Warranty and support: Check warranty terms and after-sales support* options, as this can be crucial in case of product defects or performance issues.
- Lead time and availability: Confirm product availability and estimated delivery times to avoid delays in your projects.
- Returns: Familiarise yourself with the suppliers returns and exchange policy in case you receive incorrect or damaged items.
- Delivery: Clarify delivery terms, including estimated delivery times, shipping costs and who handles insurance during transit (where applicable).
*Need help with a purchase decision? Contact us directly via chat or send an email to sales@aimsindustrial.com.au.