Choosing the Right Castors for Your Equipment
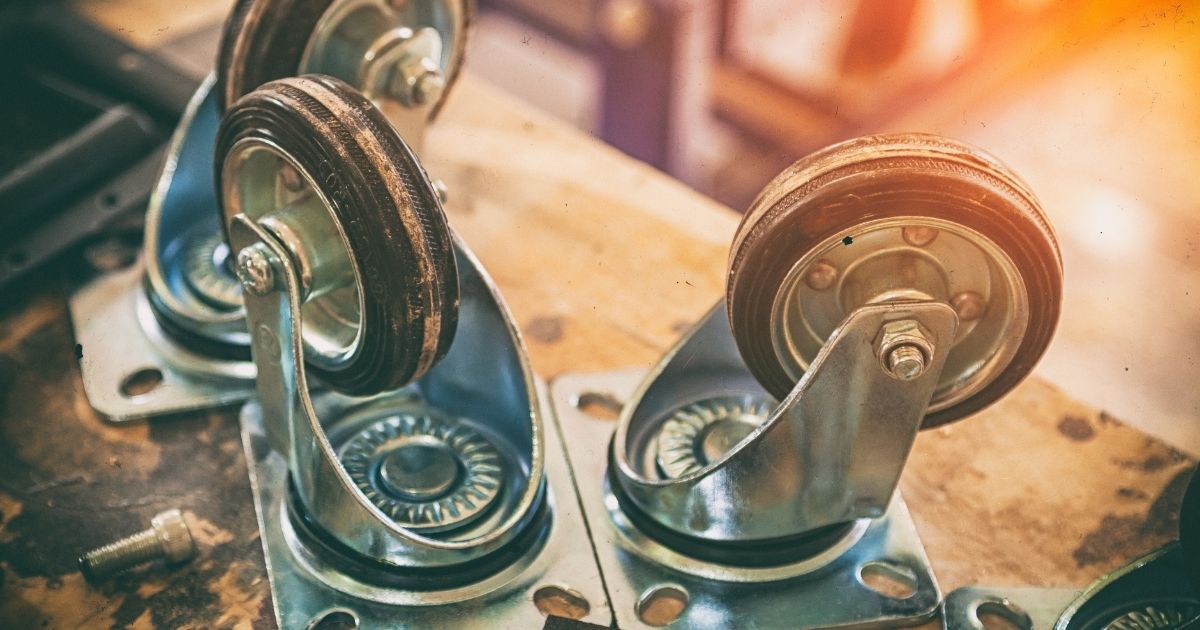
Castors (or ‘casters’) make it easy to move things around. You usually see them in an industrial setting installed on your heavy equipment and material handling tools, such as:
- Dollies, pallet jacks and trolleys
- Mobile parts washers (like the CRC SW-37 Heavy-Duty Mobile Heavyweight Parts Washer)
- Mobile workbenches and workstations
- Table carts
- Vacuum cleaners
Moreover, there are models designed for use on hospital beds and medical equipment, such as these examples from Colson, EasyRoll and Rhombus. There are even light-duty ones for light furniture such as these ones from MoveIt.
Unlike regular wheels, castors are different because:
- They may swivel via a metal frame called a fork or yoke that allows them to rotate in different directions without making the whole object turn. Some castors are even designed to lock at certain angles for stability.
- They come in different materials like rubber, plastic or metal, depending on what they are designed to roll on to (eg smooth floors, rail, rough terrain etc).
Basically, anything that needs to be moved easily and efficiently will likely have some trusty castors beneath it. They are generally sturdy, but there will be signs when it’s time to replace them.
Choosing the right castor
So, it’s time to buy new castors. These factors are crucial for ensuring smooth movement and safety for your intended application:
- Load capacity: This is probably the most important factor, so make sure the castors can support the weight of the object you will be using them on. They are typically rated for a certain weight capacity, so be sure to choose ones that exceed the weight of your object. You don’t want to cheap out on this one, or you riski a scenario where the castor breaks during a critical time or while carrying a heavy load.
Note: The weight capacity rating is per castor. So, for example, assuming the castors are mounted such that weight is evenly distributed, four similar 50-kg rated castors can collectively hold up to 200-kg of load. It would be wise to play it safe and over-specify a little, so in this case get 60-kg or 70-kg rated castors (instead of 50-kg's).
Bottom line: Do not ever overload your castors!
- Wheel material: Speaking of rolling resistance, you want to choose the type of wheel material wisely. The right material -- solid rubber, pneumatic, polyurethane, nylon, iron, steel etc -- will depend on the surface you will be using them on.
For example, castors with soft rubber wheels are good for hard floors, while hard plastic wheels are good for soft floors. You should also consider the temperature and chemicals that the wheels will be exposed to.
- Solid rubber wheels are the most common type, and they are suitable for most indoor applications.
- Pneumatic wheels have air-filled tires that provide good shock absorption, and they are ideal for uneven surfaces.
- They are much like car tires in that they have an inflatable air chamber and rubber tread.
- Polyurethane wheels are strong and durable, and they can be used on a variety of surfaces.
- Metal wheels are often used in industrial applications where heavy loads need to be moved.
Furthermore, keep in mind that there are other external variables that can affect rolling resistance, namely:
- The condition of the castor
- The condition, material and slope of the floor, including the presence of debris or slippery substances
Bottom line: Wheel material matters, as it significantly affects rolling resistance.
Pro tip: If rolling noise is a concern, then you may want to go with rubber and polyurethane wheels.
- Wheel diameter: Larger wheels offer better stability and handle rougher surfaces better, but smaller wheels are often more maneuverable in tight spaces.
Swiveling or locking: Decide if you need fixed (rigid) castors for straight-line movement or swiveling castors for turning. Double swivels offer maximum maneuverability. On the other hand, consider castors with brakes for when stopping and holding the load in place is crucial.
- Bearing type: Ball bearings offer smooth rolling and are good for light loads, while roller bearings can handle heavier loads. Sealed bearings require less maintenance and are better for dusty or wet environments. It would be wise to choose those with bearings that you can easily lubricate and replace.
- Mounting type: Choose the mounting type compatible with your equipment. Typical options include bolt-on / bolt hole mount, plate mount and stem mount.
How do you know when it’s time to replace your castors?
Visible damage:
- Cracks, chips, or breaks: Look for any visible damage to the wheels or housing of the castor. This could be caused by overloading, impact, or exposure to harsh environments.
- Flat spots or uneven wear: If the wheels are no longer round or are wearing unevenly, they won't roll smoothly and should be replaced.
- Corrosion: Check for rust or other signs of corrosion on the metal parts of the castor. This can weaken the structure and make them more likely to break.
- Loose bearings: If the wheels wobble or have excessive play, the bearings may be worn or damaged. Loose bearings can also lead to noise and decreased maneuverability.
Performance:
- Difficulty rolling: If the castors are stiff or difficult to push, it could be a sign of worn bearings, flat spots, or damage to the wheels.
- Excessive noise: Squeaking, grinding, or other loud noises can indicate worn bearings, damaged wheels, or improper alignment.
- Uneven movement: If the castors don't swivel smoothly or track properly, it could be due to worn bearings, damage, or a loose mounting.
Usage:
- Castors used in demanding applications and environments -- such as heavy loads, uneven surfaces, exposure to chemicals -- will wear out faster than those used in light-duty applications.
Manufacturer recommendations:
- Many recommend replacing them after a certain period of time or number of cycles.
By being proactive about castor maintenance and replacement, you can prevent accidents and extend the life of your equipment.
AIMS’ Note on Buying Industrial Supplies
- Breadth and depth of brands and categories: Go with a supplier that offers a wide range of reputable brands across multiple categories and sub-categories.
- Bulk purchase discounts: For large orders, check if you can take advantage of volume leverage. Some suppliers offer business accounts* that give you access to special pricing (volume discounts), preferential support and even credit eligibility (subject to supplier approval, terms and conditions).
- Product and service information: Evaluate the completeness and usefulness of data in their online product listings. Prudent suppliers will include as much useful information as possible to help you assess and compare products. In terms of service info, the supplier’s FAQs (if any) will give you a good idea of their standard policies*, processes and commitments.
- Promotions: Check for ongoing promotional campaigns so you can get the best prices. Many suppliers run regular discount-based promos. Some can point you to government-hosted rebate programmes like the SafeWork NSW $1000 Small Business Rebate.
- Safety compliance: Make sure the product in question meets Australian safety standards and regulations, especially if there are relevant compliance requirements or work health and safety (WHS) laws that apply to your business or state. Look for relevant certifications and markings where necessary.
- Supplier reliability: Choose reputable suppliers with a proven track record of delivering quality products and reliable customer service.
- Warranty and support: Check warranty terms and after-sales support* options, as this can be crucial in case of product defects or performance issues.
- Lead time and availability: Confirm product availability and estimated delivery times to avoid delays in your projects.
- Returns: Familiarise yourself with the suppliers returns and exchange policy in case you receive incorrect or damaged items.
- Delivery: Clarify delivery terms, including estimated delivery times, shipping costs and who handles insurance during transit (where applicable).
*Need help with a purchase decision? Contact us directly via chat or send an email to sales@aimsindustrial.com.au.