Choosing Between High-Speed Steel and Carbide Tools
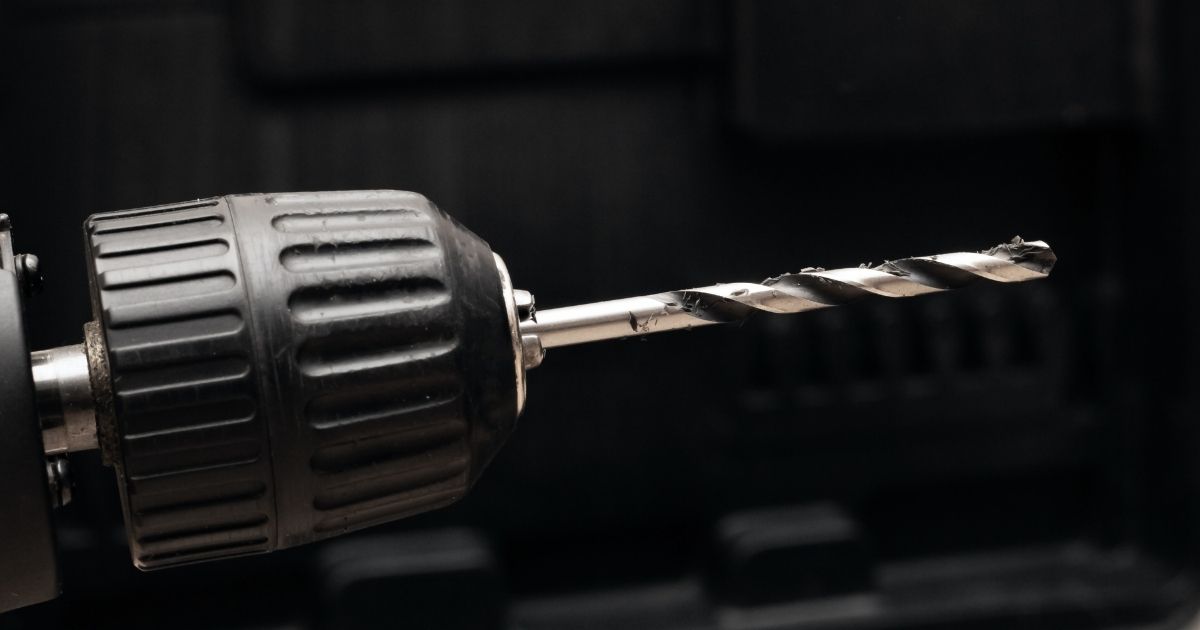
(Taken from this post by Sutton Tools. Republished with permission. Edited for point of view, recency and relevance.)
You may be wondering: “Should I use high-speed steel or carbide for my solid rotary tools, like endmills, drills and taps?”
There’s no quick answer, because there are a lot of factors involved:
- Tool size
- Depth of cutting
- Required material removal rate
- Tool life
- Cycle time
- Cost
Each type of component also presents different challenges, including design, size, batch quantity, material type and hardness.
Sutton Tools General Manager, Jeff Boyd, discusses both to help us understand when to use which one.
- Characteristics of HSS vs carbide
- HSS vs carbide for drilling
- HSS vs carbide for tapping
- HSS vs carbide for milling
- HSS powder metallurgy (HSS-PM)
HSS versus carbide: General characteristics
In general, the main characteristic of all high-speed steels is a high working hardness with excellent toughness. HSS tools also cost less than carbide tools and are often a good solution in ‘high-mix, low-volume’ applications.
Carbide is much harder, so it has a longer tool life and faster cutting data than conventional HSS. The downside of that hardness is brittleness, so the cutting edge on carbide tools can quickly fracture or chip in certain situations.
HSS can really excel over carbide due to its toughness in applications such as where:
• The component to be machined is poorly clamped
• Set-up is not rigid
• The tool is a long-reach type with excessive overhang from the tool holder
• Poor machine-spindle condition
Let’s look at three common machining operations – drilling, tapping and milling – to gain a better understanding of when to use HSS or carbide tools.
Drilling
Carbide drills are generally used for high-volume hole production, where the higher tool cost can be justified on a cost-per-part basis. For deep high-volume holes, they are often available with internal coolant ducts, resulting in longer tool life and stable production. Use of through-the-spindle and high-pressure coolant offers excellent chip evacuation, particularly in deeper holes (>3xD), and is the most effective method for cooling the edge in cut.
Carbide drilling is also the fastest way to produce holes in a wide range of metals, due to the higher cutting speeds and feeds possible. However, it’s important to know that in some higher Ni-Cr alloy steels (such as stainless steels), although the hole can be produced with high speeds, the condition of the walls of the hole can quickly work-harden. This can lead to other issues in the machining process, particularly if the hole is to be internally threaded; the tool life of the tap will be considerably shortened since it will be trying to cut through a hardened skin or surface.
Importantly, carbide tools can be justified in low-volume production for their higher hardness because they enable harder materials to be machined, potentially up to 70+HRC.
HSS drills have a very wide range of uses – from handheld applications to CNC machining in short batch runs – due to their toughness and lower cost. They are ideal for less rigid applications such as hand-held drilling, stack drilling and deep hole drilling where an internal coolant supply is not available.
There are various geometries available for specific material grades to really cut through the material and leave it in its best annealed condition. Ideal for pre-tap drilling in stainless steel, HSS drills can really benefit the life of the tap when the right geometry is used to produce the hole!
Tapping
HSS tools are typically the first choice for tapping. They are by far the most common for internal thread production, with many HSS-PM versions available more recently for the various CNC machine tapping applications, different thread types and materials groups.
Given their toughness, HSS tapping tools are also common in the Maintenance-Repair and Operations (MRO) industries, with hand taps or straight flute taps the most widely used.
HSS taps are even used in large volume applications. In difficult-to-machine material applications, HSS-PM taps are still the first choice due to the process stability they offer.
Carbide taps are not as popular due to the brittleness of carbide. It tends to chip in most tapping applications, particularly in blind holes. Carbide will fracture in steel applications at full depth, when the tap reverses and breaks the chips that were produced from the down cut in order to back out of the hole.
As mentioned earlier, HSS has superior toughness over carbide, and in the tapping process this is very important. Due to the nature of tapping being a ‘slow speed, high feed’ type process, and with the spindle slowing-then reversing at the full thread depth and breaking the chip produced from the down stroke of the machine, it’s this action that the HSS toughness characteristic performs superior to carbide.
That said, carbide taps can be used for some specific applications, including:
• Tapping hardened steel, with a specific geometry that has negative cutting angles
• Tapping high-silicon aluminium (AlSi), as the silicon content makes the material quite abrasive and carbide offers the best resistance
• Some through-hole tapping applications in steel are possible, but only with specifically suitable geometry
Carbide forming taps can also be justified in high-volume applications. Since there are no cutting edges, you can achieve long tool life without the possibility of chipping and thus justify the higher tool cost. They are quite popular in ADC12 (AlSi 8-12%) automotive aluminium applications.
Milling
Carbide endmills are by far the most popular because they offer the best Metal Removal Rates (MRR). Solid carbide endmills have become the first choice, given the variable helix designs combined with CAM packages that provide tool paths to suppress chatter from the natural vibration produced in a milling cut. Milling strategies such as trochoidal methods are now quite common.
HSS endmills still have a place, such as for manual milling machines, smaller volumes, less rigid set-ups, and the like.
HSS-PM: Best of both worlds?
As noted, conventional grades of HSS have lower cutting speeds applied, but in recent times, HSS-PM (Powder Metallurgy) has been developed to bridge the gap between HSS and carbide tools.
Simply put, HSS-PM is produced from a powder similar to carbide. This produces a finer grain structure which allows PM tools to reach a higher hardness than HSS, whilst still maintaining their excellent toughness. This means you can have a tool that will last longer than standard HSS and which can be used with high hardness materials, thereby closing the gap between the HSS and carbide tooling.
There are also some needs in rough milling applications for HSS-PM due to the heavy style of cuts taken per pass. For example, when an aerospace component has a long cycle time, producers like to run their machines ‘lights-out’ overnight to do a lot of the roughing operations. They are not, however, confident to run with carbide endmills due to their brittleness, and this is where HSS-PM roughing endmills perform best.
Whatever your application and operational considerations, it all comes down to finding the right solution.
Shop for Sutton HSS and carbide tools now.
AIMS' Note on Safe Use of Power Tools
- Inspection: Before using any tool, carefully inspect it for cracks, chips, loose handles, worn / mushroomed heads or any other signs of damage. Damaged or defective tools may cause harm! Ensure all guards are in place.
- Right tool for the job: Make sure you understand the intended purpose of each tool and choose the correct one for your specific job. Don't try to make a screwdriver work as a pry bar or a wrench as a hammer.
- Safe handling: Carry sharp tools pointed down and away from your body. Never carry tools in your pockets where they can cause injury. When passing a tool to someone, extend the handle first.
- PPE: Wear safety glasses or goggles to protect your eyes from flying debris. Consider gloves depending on the tool and task to prevent cuts or blisters but without compromising comfort, dexterity and protection. If working with noisy tools, wear ear protection.
- Maintenance: Keep your tools clean, sharp and properly maintained. Store them in a safe and organised place when not in use.
- During use: Maintain a firm grip and good balance while using the tool. Avoid distractions and focus on the task. Don't force the tool; let it work at its own pace. Keep cords clear of the cutting path and away from heat or sharp objects. Never leave a running tool unattended. When finished, turn the tool off, unplug it, and wait for any moving parts to stop completely before cleaning or making adjustments.