How Often Do You Calibrate Your Measuring Devices?
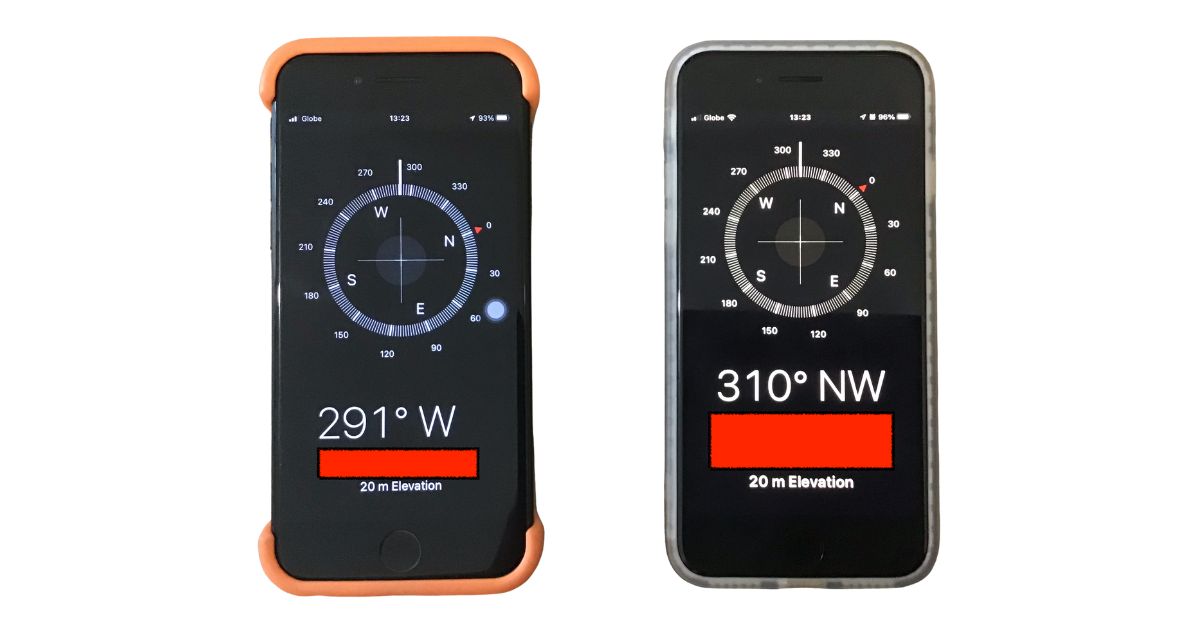
Have you tried opening the same compass app from the very same phone models only to see widely different results like this?
(It's hard to take a photo of the two phones perfectly on top of each other while showing both screens; we tried that anyway, and they still gave different angles relative to Magnetic North.)
Unless you’re relying on those compass apps to perform delicate activities (such as tactical defence operations), the difference does not seem to matter much. Nevertheless, it illustrates a point.
No two identical measuring devices will yield the “perfectly same exact” measurement all the time, but that shouldn’t stop us from using them.
(We know that those iPhones aren’t standalone compasses, but you get the point.)
We just have to trust they are giving us as accurate a measurement as possible.
Here goes the inevitable topic of calibration, and you probably know that it’s not a matter of “if”, but a matter of “when”.
More often than not, your measuring devices – be it gauges, meters, test kits or instruments of similar function – have one job: To give you accurate readings of whatever unit it’s supposed to measure.
The problem is that there are factors that could affect their accuracy, and you don’t want to risk that.
Why calibrate measuring devices?
The short answer: Because you want them to give you accurate readings all the time.
The long answer:
- Because prolonged inaccurate readings may have serious consequences
- Because you may be required by law (specifically, trade measurement laws) to keep your products true to their published measure. For example, when you manufacture and retail a variety of products (eg. packaged/processed food, raw food, petrol etc)*
- Because even minor out-of-tolerance outputs can have major negative effects when left unnoticed and not corrected immediately
- Because your customers don’t want to feel like they’re being ripped off
In more practical terms, you want to have your measuring devices calibrated:
- To account for wear and tear of its mechanical and electronic components
- To ensure its accuracy, and therefore, reliability
- To ensure its reading doesn’t deviate too much from standard tolerances
- To ensure its reading is consistent with other measuring devices
- To keep it from having performance discrepancies
Put simply, it’s just not possible to keep your gauges and meters performing at 100% of its designed accuracy and efficiency forever, as there are several external factors that could affect its accuracy.
When to consider calibration
As a minimum, Go Calibration recommends calibrating your instruments at least once a year “to ensure accuracy and provide quantitative data to ensure you can provide quality assurance for your customers.”
(If you want an exhaustive list of calibration schedules for various equipment, here’s the National Association of Testing Authorities (NATA) Calibration reference equipment table as of September 2020.)
Furthermore, here are instances when it’s a good idea (and even advisable) to have your measuring device checked for accuracy earlier than your scheduled annual check:
- When it is recommended by the manufacturer: There's a good chance that they have indicated in the owner’s manual their recommended calibration intervals, which could be more than once a year depending on various conditions. Use that schedule as your first reference when deciding whether you should have the instrument checked more often.
- Before you go on planned maintenance downtime: You’ll be shutting down operations to do routine checks and perhaps even inventory management. You’re probably even scheduled to replace components, parts and consumables (eg. lubricants) for preventative maintenance. You might as well use this time to have your measuring devices checked, so that you are confident that everything is in tip-top condition when you put them back together.
- Before you use them in a critical measuring project: This is especially important if you plan to make decisions based on the instrument’s readings. You want to be confident with its measurement results, especially if it will influence strategic action plans. For example, when it’s time to get checked for certifications.
- Before you undergo mandatory audits or inspections: Some industry regulators and federal authorities, such as the National Measurement Institute, subject businesses to audits and inspections in compliance with trade measurement laws.
- After a potentially damaging incident: While many measuring devices come in heavy-duty casing and built with internal overload protection mechanisms, there are occasions when its measuring integrity may have been compromised, such as (1) after being subject to mechanical and electrical shocks or (2) after taking physical damage, such as from an accidental drop.
- After being exposed to extreme humidity and temperature: Yes, these environmental factors can affect the accuracy of your gauges, even when they are sealed and designed for outdoor use. There are, however, some instruments that are specially designed to take much more humidity and temperature levels and fluctuations than their ordinary counterparts.
- As the instrument ages: The longer the instrument is in service, the more often you may need to have it calibrated, to account for wear and tear, until they are due for complete replacement.
Put simply, as this US Navy video explains: “Like components, test equipment itself decays” and “without calibration, our costs [can] go up and our tactical efficiency goes down."
Measuring devices we can help you calibrate
Unless you’re a certified metrologist with the proper equipment and facilities, you are usually best to leave calibration to the pros.
We can help you keep these instruments accurate:
- Backflow Test Kit
- Bore Gauge
- Centrifuge (RPM)
- Conductivity Meter
- Depth Gauge
- Dial Gauge (Mechanical/Digital)
- External Micrometers
- Height Gauge
- Metal Detector
- Micrometers
- pH Meters
- Pressure Gauge
- Pressure Transducer
- Tachometer
- Temperature Enclosure
- Thermometer
- Tyre Inflation Gauge
- Vacuum Gauge
- Vernier Calliper
In a nutshell
We hope this article served as a quick but practical reminder that:
- There’s no one-size-fits-all schedule to calibrate your measuring devices.
- A wise way to comply with applicable trade measurement laws is to keep your measuring devices calibrated.
- Wear and tear, extreme ambient factors and mishandling can affect your measuring devices' accuracy.
- As a minimum, have your measuring devices calibrated once a year.
- If in doubt, don’t wait and just have them checked.
- You can’t DIY the calibration, so leave it to the pros.
- We can help you calibrate your gauges - let's talk via chat or email.
AIMS’ Note on Buying Industrial Supplies
- Breadth and depth of brands and categories: Go with a supplier that offers a wide range of reputable brands across multiple categories and sub-categories.
- Bulk purchase discounts: For large orders, check if you can take advantage of volume leverage. Some suppliers offer business accounts* that give you access to special pricing (volume discounts), preferential support and even credit eligibility (subject to supplier approval, terms and conditions).
- Product and service information: Evaluate the completeness and usefulness of data in their online product listings. Prudent suppliers will include as much useful information as possible to help you assess and compare products. In terms of service info, the supplier’s FAQs (if any) will give you a good idea of their standard policies*, processes and commitments.
- Promotions: Check for ongoing promotional campaigns so you can get the best prices. Many suppliers run regular discount-based promos. Some can point you to government-hosted rebate programmes like the SafeWork NSW $1000 Small Business Rebate.
- Safety compliance: Make sure the product in question meets Australian safety standards and regulations, especially if there are relevant compliance requirements or work health and safety (WHS) laws that apply to your business or state. Look for relevant certifications and markings where necessary.
- Supplier reliability: Choose reputable suppliers with a proven track record of delivering quality products and reliable customer service.
- Warranty and support: Check warranty terms and after-sales support* options, as this can be crucial in case of product defects or performance issues.
- Lead time and availability: Confirm product availability and estimated delivery times to avoid delays in your projects.
- Returns: Familiarise yourself with the suppliers returns and exchange policy in case you receive incorrect or damaged items.
- Delivery: Clarify delivery terms, including estimated delivery times, shipping costs and who handles insurance during transit (where applicable).
*Need help with a purchase decision? Contact us directly via chat or send an email to sales@aimsindustrial.com.au.