Your Complete Guide to Choosing Industrial Suppliers in Australia
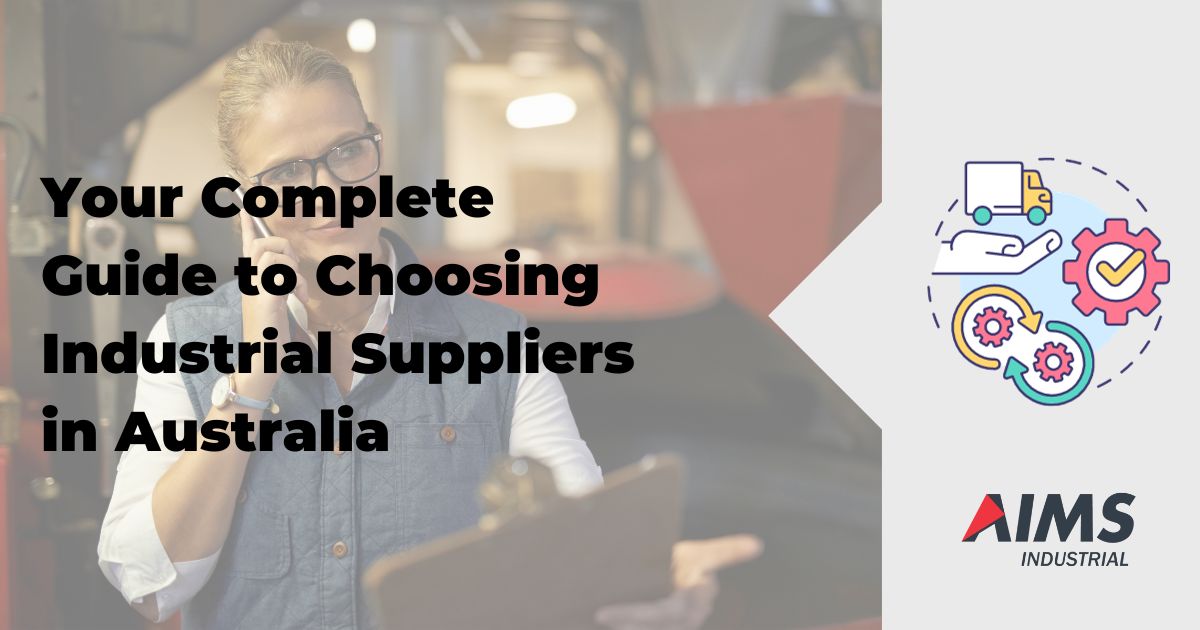
Selecting the right suppliers for your industrial supplies can significantly affect your costs, operations and overall success. Here is a comprehensive list of factors to consider and questions to ask when making this important decision for your business.
- How many suppliers do you really need?
- Qualities of a reliable supplier
- Most common challenges in maintaining good inventory
- Managing your inventory to avoid unplanned downtime
- The price-vs-quality compromise
- Library of guides to help you make informed buying decisions
- Benefits of having a buyer account
How many suppliers do you really need?
“Too much of anything is good for nothing,” according to a proverb. But is it really, especially when you talk about suppliers?
There are upsides to professionally managing your inventory of materials and equipment, and it follows that you want to have the right supplier(s) for them. Inevitably, it begs the question:
- In a small-to-medium enterprise (SME), should you have a single, exclusive supplier, or should you work with multiple suppliers at once?
There are obvious benefits to both options, and the right answer for you will largely depend on the complexities of your organisational structure and requirements.
Moreover, here are other considerations that also factor into your decision:
- Complexity of systems: You’re working with multiple third parties and factoring them into your processes. When you have to deal with multiple data in different formats, systems integration becomes more challenging.
- Consistency in quality: With multiple suppliers, you can expect to see variations in quality that gets more challenging to manage. On the contrary, production is relatively simplified when you use just one supplier, because you are most certain that their components went through the same QC process.
- Cost of freight: The more a supplier is delivering in one shipment, the lower the freight cost per item. In some cases, they may even charge no freight at all, depending on the amount and/or volume of orders. You can use this to your advantage when you order in bulk.
- Downtime: When your supplies short supply, it may stop production, which clearly puts you in a difficult position in many respects (such as impacting your service level agreements with your clients and partners, and losing market share due to delayed manufacturing output).
Having a close relationship with one or two suppliers has distinct benefits, but there are also risks in putting all your eggs in one basket. It’s all about striking a balance based on the idiosyncrasies of your business.
As a general rule, you should have a primary supplier and at least one secondary supplier.
What matters most is that you are confident that they can be a reliable partner for your business.
Qualities of a reliable supplier
You only want to buy from suppliers who can provide high-quality products and dependable service at competitive prices, as that brings a multitude of advantages, to your business. Here is a checklist to use to evaluate your shortlist of suppliers to make sure you’re getting as much benefit from them:
Industry expertise: A good supplier will understand your specific requirements enough to be able to give you product advice. Their front-liners can communicate with you in the context of industrial, manufacturing and engineering perspectives.
- Do they have product specialists that really understand the technical specifications of the products they sell?
- Do they take the time to help you identify the products you need?
- Do they comply with all relevant industry standards and regulations?
- Do they have a demonstrated track record of supplying for businesses similar to yours?
Product range and quality: A good supplier will help you save time, especially if they can provide all the supplies you need from the brands that you trust. As you get your components, parts, materials and equipment from the same proven source, you worry less about getting sub-standard output that’s prone to costly defects, returns and customer complaints.
- Do they offer the full range of core industrial supplies you need -- including capital goods and equipment, components, consumables, safety gear and tools?
- Do they offer all the major product categories that you need?
- Do the brands they carry have a good reputation for quality, reliability and compliance to industry standards?
- Do their product listings provide accurate and essential information to help you make an informed decision about the purchase?
- Do they have a quality control system to ensure you get the products right according to specifications before dispatch?
- Do they source hard-to-find and off-the-shelf items?
- Do they have a support team which will provide Safety Data Sheets when requested or promptly handle warranty issues, should they arise?
Supply chain and logistics management: A good supplier is well-connected with manufacturers, distributors and importers, thus enabling competitive wholesale and retail prices to your benefit.
- Do they have reliable logistics and order fulfillment partners to deliver your orders with care and on time?
- Do they have sensible foresight on product demand, availability cycles and pertinent logistical challenges?
- Do they have enough inventory levels to accommodate your just-in-case (JIC) or just-in-time (JIT) requirements?
- Can they handle cross-border / overseas shipments?
Pricing competitiveness and transparency: A good supplier should be a partner and give you fair prices and never try to rip you off.
- Do they display clear pricing information in their store and quotes?
- Do they go out of their way to offer you products with the best prices?
- Do they comply with fair trade regulations?
- Do they offer volume discounts?
- Do they offer preferential pricing?
- Do they offer flexible payment options (cash, card, cheque, bank transfers, PayPal and in-house credit*)?
- Do they offer flexible payment terms?
- Do they have hidden charges?
- Do they charge handling fees?
- Do they price-match?
Delivery in full, on-time (DIFOT): A good supplier understands that they need to get you the products on time, as delays could have undesirable consequences that affect the timeliness of your operations.
- Do they clearly communicate and display estimated lead times, delivery speeds and dates when ordering?
- Do they dispatch and deliver the goods and services according to agreed-upon schedules?
- Do they always have stocks of high-demand and fast-moving products, especially consumables?
- Do they have sound inventory management practices and order tracking systems?
- Do they work to meet tight delivery requirements within reasonable short notice?
Customer service: A good supplier cares enough to try to really understand the intricacies of your business and go out of its way to help you.
- Do online reviews suggest that customers are generally happy with the service and support they provide?
- Do they promptly address quality issues and take quick action to resolve them?
- Do they promptly respond to your pre-sales and post-sales enquiries?
- Do they promptly communicate possible and actual bottlenecks that could affect delivery dates?
- Do they have quick turnaround for enquiries that require contacting you for updates?
- Do they pay your site a visit -- where possible, even just occasionally – in the name of building rapport?
- Do they charge extra to offer customer support?
- Do they support warranty coverage?
- Do they offer easy returns?
Most common challenges in maintaining good inventory
Inconsistent tracking systems: Some businesses still implement very little inventory tracking, while some overdo it with multiple software platforms. This usually happens when manufacturers, distributors, partners and vendors use different supply chain management platforms. Unfortunately, that often results in different data sets with incompatible taxonomy that end up under-utilised in data silos. Depending on the size of your organisation, you may consider centralising your processes, at least internally, by investing in a highly flexible enterprise resource planning (ERP) platform. From there, you can standardise some internal processes and taxonomy (eg SKUs) across the board.
Inaccurate, outdated data: While not absolutely unavoidable, inaccuracies in data may be kept to a minimum by continually ensuring that the attributes of materials and equipment are updated in line with supplier advice. As demand changes, so do the availability and prices of raw materials, commodities and services, so don’t rely on your suppliers to keep you informed. Someone in the organisation needs to continually request updates.
Manual documentation: Some will argue the merits of managing inventory the "old school” spreadsheet way. It may work for you if you can afford the time (and thus, productivity loss and manhours) to do it repeatedly and scalably, however there's always the challenge of manually updating your data every single time there is movement in your stock. In this age of specialised software-as-a-service, spreadsheets are considered "legacy and traditional" and very limited in capability. And, we're not even talking about Industry 4.0 Internet of Things (IoT) enabled inventory.
Damaged assets: This is where you start asking questions such as:
-
Was this damage caused by the manufacturer?
-
Why didn't we see the defects earlier?
-
Is it replaceable?
-
Is it repairable?
-
How much will it cost to repair?
-
How soon can we get it to work?
-
How will this affect the pipeline?
Misplaced assets: Issues begin to get real once you're on the floor looking for the actual equipment that, on paper (or software), was "supposed to be somewhere here". Not every business can afford to tag NFC and RFID trackers to every piece of equipment in order to know its whereabouts at every moment. Now there are even more questions:
-
Was it actually received in the warehouse?
-
How long has it been missing?
-
Did we store it in the wrong location?
-
Do we even have an asset checkout process?
-
Did someone check it out? Or ...
Theft: This is unfortunately not uncommon.
- Did someone take it without permission?
- Who's supposed to be looking after it?
Under-utilised or inefficient warehousing: Just stock up a lot of everything and we're good, right? If you thought over-stocking is always a good thing, think again. Here are some factors to consider:
- Some materials require special storage within a certain level of humidity and temperature.
- Materials become obsolete.
- Materials deteriorate.
- Materials expire.
Managing your inventory to avoid unplanned downtime
You expend a lot of resources to build your business and make sure it's in good shape, and costly major inconveniences caused by equipment malfunctions and a limited supply of materials are the last things you need. The good thing is that it's totally avoidable, thanks to inventory management.
Different sources will give you different definitions on what are the types of inventory, but we'll stick with three main types according to business.gov.au:
- Raw materials
- Work-in-process
- Finished goods
*Some sources include MRO as a fourth main type, and some even expand the list to as many as 13 types. In many context, inventory management means making sure they have sufficient materials and equipment to keep their business operational. When talking about inventory, people usually think of trading stock, which is essentially any component a business "acquires, produces or manufactures, for the purpose of manufacturing, selling or exchanging", according to Business.GOV.AU.
Often, they are referring to materials, which are components used in the manufacturing of the product. Common examples include:
- Bearings, belts and pulleys installed as parts of a power transmission system
- Bolts and nuts used to affix parts and surfaces
- Greases, lubricants and oils applied to avoid friction between moving parts in a system
- Paints applied as a protective layer onto surfaces
Then, there’s equipment, which are apparatus, machinery and tools to facilitate the manufacturing of the product. Common examples include:
- Power tools to make various manual processes (eg cutting, drilling, grinding etc) way easier for the human hand
- Measuring tools to determine the physical dimensions of objects
- Polishing compounds to apply a finish to surfaces
To keep it simple, we'll focus on one of the main benefits of proper inventory management -- which is avoiding unplanned downtime.
The list of why unplanned downtimes happen ranges from reasons beyond your control:
- Global supply chain and logistics issues
- Business closure due to severe weather
- Supplier partner issues
- Power outage
… to scenarios that could have been avoided, since they are within your control:
- Ineffective business continuity plan (or lack thereof)
- Process failure due to machine and/or human error
- Equipment failure
- No supply of materials and parts due to insufficient planning and inventory
Being in the industrial and engineering supplies business, we've seen first-hand the undesirable effects of unplanned downtimes to our customers:
- On a business level: It’s hard to play catch up when unexpected cost and workforce burden start piling up, not to mention the possible consequences to your production output and revenue.
- On a department / functional level: The guys in MRO and Purchasing work under time pressure to restore up-time and manage backlogs.
- On the production floor: The workers scramble to meet even tighter deadlines, thereby increasing the risks of errors.
While unplanned downtimes can happen for reasons beyond your control, you can mitigate some risk through proper inventory management.
- Use a comprehensive, consolidated database to track your assets: It does not have to be a complicated software platform that no one in your business knows how to operate, so long as it is useful to your staff.
- Delegate the task to a specific person: Where appropriate, assign or hire an inventory specialist to own the process. Ideally, he/she understands supply chain management and can maintain productive relationships within your team and with your partners and suppliers.
- Purchase in bulk: Where applicable, evaluate if you can benefit from volume discounts, provided you find a supplier that offers special pricing for bulk orders. Remember to take into account your storage / warehousing capacity and the expiration dates of the products you want to store (if applicable).
- Monitor usage: Know what you have right now, what you'll need soon and who will use it. Over time, you will be able to identify patterns from which you can work to optimise supply replenishment strategies.
Once the platform and people are in place, it's time to start tracking your assets. Important data to record could include:
- Unique identifiers [eg serial numbers, stock keeping units (SKU), universal product codes (UPC) etc]
- Make and model
- Item description
- Supplier and/or manufacturer
- Purchase cost
- Purchase date
- Lifecycle / Shelf life
- Condition of the item as of [date]
- Quantities on hand
- Special storage requirements (including hazardous material info for proper handling)
- Warranty information
- Maintenance requirements and schedule
- Checkout details (who's using it where and when)
- Safety data sheets
- Technical data sheets
- Use only high-quality products: The more durable your components are, the longer you can use them. This is especially critical for equipment parts that are hard to replace, thereby risking unplanned downtime once the machine stops working.
Nevertheless, products of superb quality often come at a price. Should you just go for low quality products and just replace them often?
The price-vs-quality compromise
"Hi, AIMS Industrial Supplies! I’m looking to replace the [component/material/part] in my [machine/system]. I want something that is cheap and long-lasting. What are my options?”
Arguably, there is no standard response to the question. To many people, “cheap” and “long-lasting” seldom go together in the same sentence; the consensus is that nothing cheap lasts long.
Instead, you should consider these factors when you’re faced with the price-quality dilemma as a customer:
- Is it a component of a mission-critical system?
- Will its durability affect other parts?
- How much professional labour do you need to hire to get the job done?
- How much time and money does it cost to replace?
- How much unexpected downtime can you afford?
- Are you okay with original equipment equivalents (OEE)?
- Are you okay with shorter warranty periods?
The answer is very subjective to your budget, preference and how many of those factors you are willing to compromise on in exchange for paying less money.
Here are some scenarios that are very relatable, especially if you’re in MRO, where the predictability of service intervals and risks of unplanned downtime easily become a key concern when there is the premature failure of a part.
- Bearings: It’s easy to dismiss these rollers as mundane parts until one of them breaks. The cheaper ones can easily wear out, especially if they are carrying heavier loads than they are weight-rated for. It only takes a broken bearing or two to halt an entire conveyor belt system. Even when you immediately have a spare unit on hand, it may take an hour or more to replace it.
- Belts: Although cheaper industrial belts are known to wear out faster, some people still buy them, and in bulk even. They argue the part is relatively easy to check for damage and replace anyway. The problem is when these belts snap at the wrong place and time, it can damage other parts. As an aside, another shortcut people like to take with belts in order to save money is to only replace damaged ones. If there are multiple belts on a single pulley, they should all be replaced by the same brand at the same time. Replacing only one or two belts will cause uneven load and wear and cause all the belts to wear out more quickly, which will ultimately be more costly.
- Hoses, ducting and fittings: While these components are designed to handle various loads of pressurized and non-pressurized liquids or gases passing through, sometimes 24/7, it’s hard to guarantee that the entire system is fully efficient. Inevitably, there will be leaks due either to wear and tear or just plain defective or low-quality components. When something breaks or leaks, however small, the whole system stops working as intended. Aside from low-quality components, you should also consider low-quality workmanship, so it pays not to cheap out on labour for installation and repairs done right by competent professionals. For some systems, especially pressurized ones, such as air-conditioning units, you will have no choice but to spend extra to replace leaked refrigerants.
- Roller chains: Their prices vary wildly and are usually influenced by the quality of materials and the processes involved in manufacturing (and which country they were manufactured in). Also, they can get expensive quickly as they’re usually sold by length (eg. boxes of 10 ft etc.). Some brands of chains are more sought after than others, despite their heftier price tag, simply because of their reputation for superior reliability, easier serviceability and the longer service life they can provide. Some of the higher end chains are also self-lubricating and extremely pricey but have obvious benefits. To MROs, the longevity of the pricier product alone saves them hours of downtime since they don’t have to service the machine as frequently.
- Slip resistance products: Depending on the size and type of surface you need to install anti-slip products onto, you might be tempted to go for cheaper solutions so you can cover more area. After all, your workers are already wearing slip-free boots anyway, right? That’s a common argument from customers, until they realize it’s often very cost-effective to install custom-sized ladder rung covers, safeplates, safety matting and stair nosings because of their longevity alone.
As a consumer, you might even think that the higher the price of the product or service, the higher its perceived quality, which are both acceptable marketing psychology and buyer heuristic.
As we always say, err on the side of caution. You get what you pay for.
Your One-Stop Library for Industrial, Maintenance and Safety Insights and Updates
Buying industrial and engineering products can be tricky, especially for beginners and the uninitiated. While a good supplier will have capable product specialists to assist you in your purchasing journey, you’d still want to do some preliminary research.
- How do you choose one product over the other?
- How do you get the measurements and specifications?
- What specific factors should you consider when buying a certain product?
- Where do you even start your research?
A good supplier gives you the knowledge to make informed buying decisions.
Make sure to check out our content library designed to help you:
- Make wise purchasing decisions
- Stay safe and compliant with Australian safety standards
- Stay productive in your trade or profession
- Keep your chores and hobbies interesting
- Help your peers by sharing your experience and expertise
We update this list regularly so bookmark this page or subscribe to our newsletter, if you’d like to be notified when something new comes up.
Benefits of having a buyer account
A good supplier gives you the option to create an online account so you can enjoy these benefits 24/7 from the convenience of your laptop or smartphone.
Shop and make informed buying decisions:
- Browse through their full range of products
- Download related catalogues, data sheets and user guides
- View accurate and comprehensive product information on the product(s) you want to purchase
- See product reviews from other customers (or write one for products you've bought)
- Save your favourite products for purchase later
Manage your transactions:
- Access, approve and manage your quotes, invoices and orders
- Place your orders
- Re-order products you've bought before
Make easy and secure payments:
- Pay for your orders and invoices with peace of mind via secure payment channels
- Pay in installment via PayPal or in-house credit (provided you meet certain requirements and a minimum monthly spend)
- Enjoy exclusive discounts and first dibs on newly listed brands and products
- Get special pricing and volume discounts
We hope you found this guide helpful, and you are now more confident when planning and purchasing industrial supplies for your business.
If you need help, please do not hesitate to reach us via chat email at customerservice@aimdindustrial.com.au.