Quick Guide to Stainless Steel Fasteners
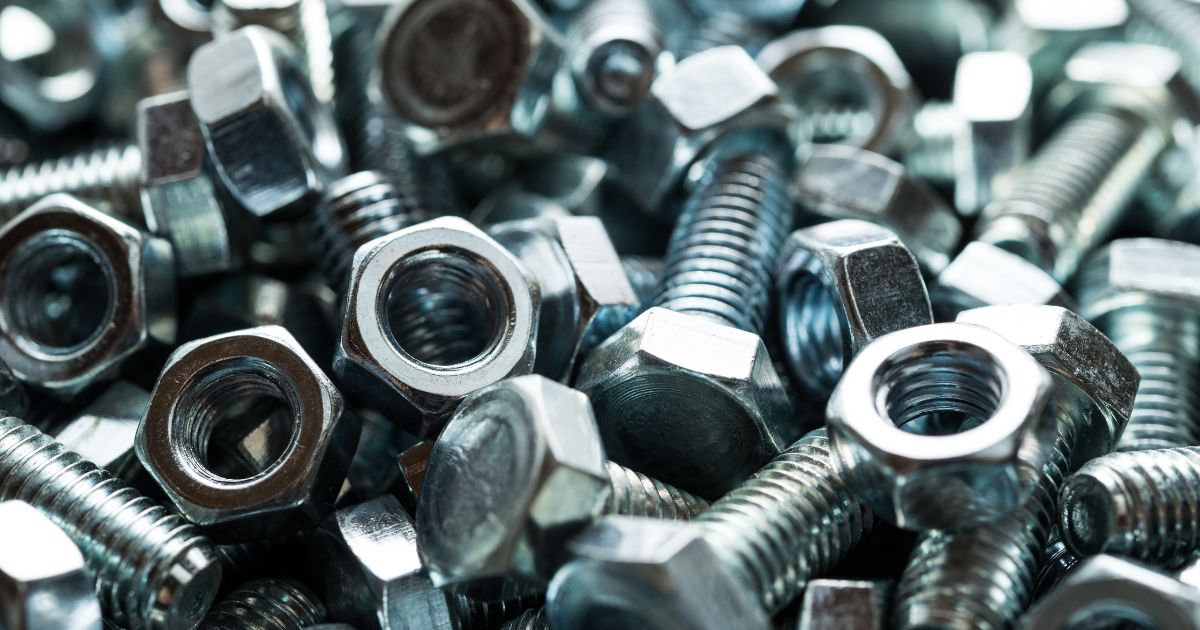
Are you working in a caustic environment where corrosion is an important factor in material selection? Are you concerned about rust forming on structural parts and fasteners due to a wet or moist environment?
If so, then fasteners made of stainless steel may be the answer to your problem.
Many people ask us these questions:
- Which is better between 304 and 316 stainless steel fasteners?
- What's the difference between 304 and 316 stainless steel?
- Why does rust still form around stainless steel?
- Is 316 stainless steel suitable for seawater immersion?
- Is well-polished stainless steel maintenance-free?
We hope this article gives you a basic understanding of stainless steel and the best choice for your intended use, especially when it comes to fasteners.
(We also updated it to cover some common misconceptions about stainless steel in general, courtesy of our friends at Hobson.)
What is stainless steel?
Stainless steel is a low carbon alloy with at least 10.5% chromium, as well as other alloying elements such as nickel and molybdenum, which enhance the anti-corrosive properties of the material. At or above this level of chromium, a layer of complex chrome-oxide forms on the surface which prevents oxygen atoms from penetrating the steel, thus preventing the formation of iron oxide (rust).
The chrome-oxide layer is what makes the stainless steel "stain less".
Does stainless steel rust?
Rust may still form on the surface and in crevices, especially when you choose the wrong grade of stainless steel for the application.
Put simply, using stainless steel does not guarantee that minor surface rust will not appear.
It is actually quite common, particularly in harsh environments, to see “tea stains” on the surface of stainless steel, where a small amount of surface rust has formed.
When it comes to stainless steel fasteners, it is critical that the rust does not penetrate the body/structure, to maintain its integrity.
According to Australian fastener manufacturer Hobson Engineering: If rust occurs within a few days or weeks, it is almost certainly due to carbon steel contamination from fabrication or the local environment. Longer initiation periods arise from:
- Surfaces that are too tough
- Aggressive environments (eg. 304 SS posts on a wharf)
- Lack of washing (eg. drainpipes under eaves)
What are the types of stainless steel?
Stainless steel comes in various types, based on the ratio of the alloying elements and on the molecular structure of the material.
The four fundamental types of stainless steel are:
- Austenitic stainless steel
- Duplex (austenite-ferrite) stainless steel
- Ferritic stainless steel
- Martensitic stainless steel
(For more information on the family of stainless steel, please refer to The Atlas Steels Technical Handbook of Stainless Steels.)
What about stainless steel grades?
The grade determines the corrosion resistance, durability, temperature resistance and other essential characteristics of the material.
Different grades have different ratios of chromium, nickel, molybdenum and carbon.
Stainless steel grades define how the product will perform in each environment; hence it is very important to know which grade is appropriate for your intended use.
The typical grades you'll encounter in your search are the 200 and 300 series. The 300 series is the most common. Specifically, 304 and 316 (also known as A2 and A4 grades, respectively).
304 stainless steel
Grade 304 (UNS 30400) is the most common and widely used of the 300 series. It has 18-20% chromium and 8-12% nickel. It is sometimes called the standard 18/8 austenitic stainless steel.
It is resistant to oxidation and corrosion and is best used in food preparation and processing environments, and when aesthetics is important. This is the one commonly used in general workshop and household stainless steel hardware.
Benefits:
- Ease of fabrication
- Ease of cleaning
- Helps prevent product contamination
- Offered in various finishes and appearances (eg. in hinges & locks)
Commonly used in:
- Auto mouldings, accent trims, intake and exhaust manifolds, wheel covers etc
- Corrosion-resistant electrical enclosures
- Hose clamps
- Kitchen equipment
- Pressure vessels
- Piping
- Storage tanks
316 stainless steel
Grade 316 (UNS 31600) is also referred to as, in the vernacular, “marine grade stainless steel”, although the term is not a recognised industry standard. It has the addition of 2-3% molybdenum. The chromium content is lowered to 16-18%, and the nickel content is raised to 10-14%.
This change in the chromium-nickel ratio and the addition of molybdenum significantly increases the metal’s resistance to “salt” corrosion.
This makes 316 a very heat-resistant stainless steel with superior corrosion resistance as compared to other chromium-nickel steels when exposed to many types of solutions such as seawater and brine.
It may cost a little more, but that translates to savings in the long run, especially if your fasteners and structures are going to be used outdoors.
It also has greater resistance to many chemicals than Grade 304.
Benefits:
- Ease of fabrication
- Ease of cleaning
- More resistant to common solutions (sulfuric acid, chlorides, bromides, iodides and fatty acids at high temperatures)
- More protection against seawater and brine
Best used in:
- Marine construction
- More corrosive environments where the material will be exposed to chemicals and solvents
Important: While 316 is often referred to as “marine grade”, it simply means that it will remain bright and shiny, provided it is maintained properly. It may still rust (especially in crevices) when exposed to seawater, which has about 20 times the chloride level 316 is designed to withstand.
Stainless steel properties
Stainless steel has these following characteristics that -- depending on your intended purpose – may or may not be to your benefit.
- Better aesthetic appeal
- Better durability
- Better resistance to corrosion
- Better resistance to extreme temperatures
- Better resistance to oxidation
- Harder to weld
- Higher work hardening rate
- Higher cryogenic toughness
- Higher tensile strength
- Lower electrical conductivity
- Lower heat conductivity
- Lower magnetic response
- More brittle (and therefore may be prone to denting)
- More expensive and time-consuming to manufacture
*Versus other common metals
Note: Higher tensile strength fasteners may not be available or, if they are, can be very, very expensive. For more information, here’s a related article discussing high tensile bolts.
Should you use 304 or 316 stainless steel fasteners?
The most common grade is 304 stainless steel, but there will be certain situations where 316 is your best option.
If you work in an environment where there is exposure to chlorine in the atmosphere and other corrosive substances, choose 316 stainless steel.
Just keep in mind that, while it’s more rust-resistant than 304, it is more brittle because of its chemical make-up.
Elsewhere, you may opt for 304 since it also serves the purpose of basic corrosion protection.
In a nutshell:
AIMS’ Note on Buying Industrial Supplies
- Breadth and depth of brands and categories: Go with a supplier that offers a wide range of reputable brands across multiple categories and sub-categories.
- Bulk purchase discounts: For large orders, check if you can take advantage of volume leverage. Some suppliers offer business accounts* that give you access to special pricing (volume discounts), preferential support and even credit eligibility (subject to supplier approval, terms and conditions).
- Product and service information: Evaluate the completeness and usefulness of data in their online product listings. Prudent suppliers will include as much useful information as possible to help you assess and compare products. In terms of service info, the supplier’s FAQs (if any) will give you a good idea of their standard policies*, processes and commitments.
- Promotions: Check for ongoing promotional campaigns so you can get the best prices. Many suppliers run regular discount-based promos. Some can point you to government-hosted rebate programmes like the SafeWork NSW $1000 Small Business Rebate.
- Safety compliance: Make sure the product in question meets Australian safety standards and regulations, especially if there are relevant compliance requirements or work health and safety (WHS) laws that apply to your business or state. Look for relevant certifications and markings where necessary.
- Supplier reliability: Choose reputable suppliers with a proven track record of delivering quality products and reliable customer service.
- Warranty and support: Check warranty terms and after-sales support* options, as this can be crucial in case of product defects or performance issues.
- Lead time and availability: Confirm product availability and estimated delivery times to avoid delays in your projects.
- Returns: Familiarise yourself with the suppliers returns and exchange policy in case you receive incorrect or damaged items.
- Delivery: Clarify delivery terms, including estimated delivery times, shipping costs and who handles insurance during transit (where applicable).
*Need help with a purchase decision? Contact us directly via chat or send an email to sales@aimsindustrial.com.au.